Mechanical Surface Layer Strengthening
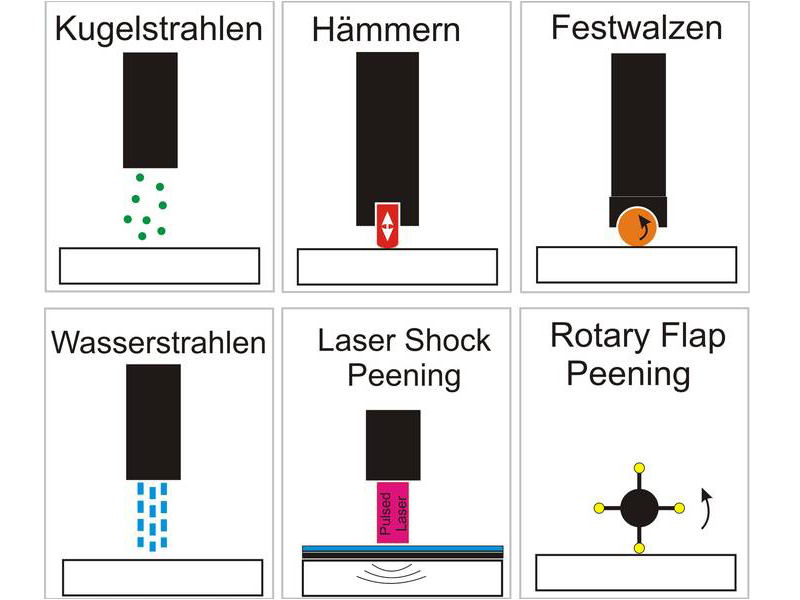
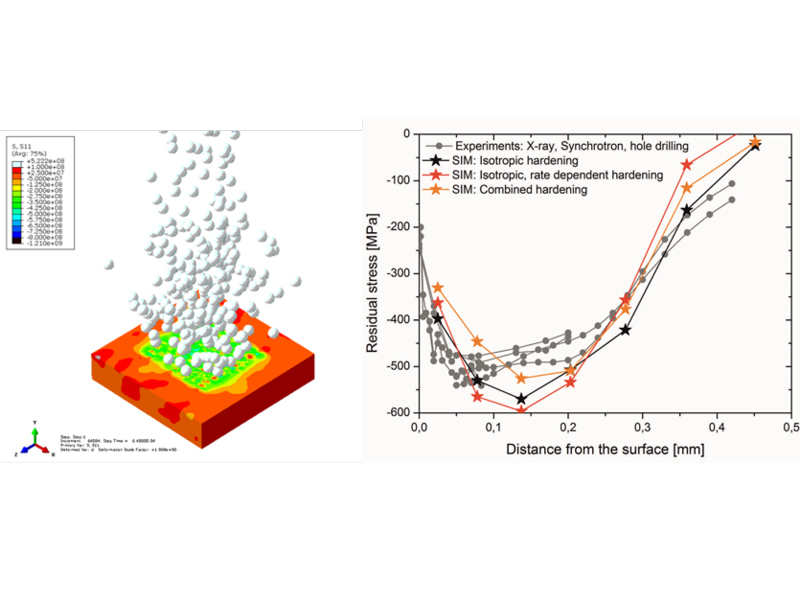
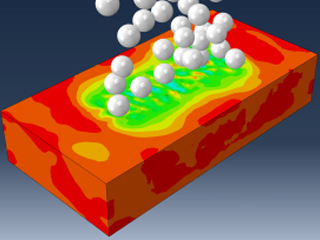
The surface layer of metallic components and structures is of decisive importance for their lifetime. In all industrial sectors, where components are exposed to high stress such as automotive, vehicle and railway construction, aerospace, steel and bridge construction, drive technology and gear manufacturing, combustion engines, steam and gas turbines, compressor and pump manufacturing, tool and mold making as well as medical engineering, the material condition of the surface layer plays an elementary role. The reason for this is that damage processes such as fatigue and corrosion often initiate at the surface. Hence, they can be retarded or accelerated depending on the stress state of the surface layer, which has a significant impact on the component lifetime.
A lot of mechanical surface treatment methods (Figure 1) have been developed during the recent decades. These methods use the effect of the elastic-plastic deformation of the surface layers of metallic components by use of suitable impact tools such as balls, hammers, rollers, waterjet and laser. This deformation results in strengthening and compressive residual stress in a thin surface layer. Such beneficial layers may serve the purpose of significantly increasing the fatigue resistance of the entire component.
Therefore, we develop material models and simulation tools which help to optimize the material behavior and the component lifetime by use of a customized surface treatment. We derive correlations between material behavior, component geometry and process-related influencing factors of mechanical surface treatment methods on the residual stress field and the surface layer strengthening by combining experimental results with material and process simulation. Finally, we determine the increase of lifetime of cyclic loaded components as a function of the process parameters.