Making extremely thin lubricating films predictable — extension of the Reynolds equation by a non-linear wall slip law
Many tribological systems are operated at their load limits for reasons of efficiency. Lubrication gaps are becoming narrower and lubricating films must withstand greater loads. For the reliable design of such systems, development and construction depend on precise calculation methods. However, conventional calculation approaches fail when it comes to so-called boundary lubrication. Prof. Michael Moseler and Dr. Kerstin Falk from the Fraunhofer Institute for Mechanics of Materials IWM in Freiburg have succeeded in clarifying the mechanisms of boundary lubrication and making them predictable. This opens a path to new design possibilities for high-performance tribosystems. They present their groundbreaking approach in a renowned scientific journal.
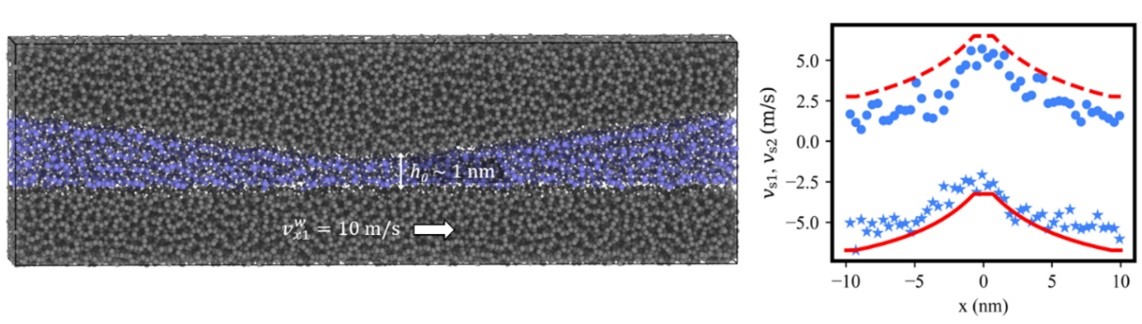
When an electric vehicle accelerates, the motor generates maximum forces and enormous pressures act on the gears of the electric drivetrain. Surface meets surface, metal meets metal. If there were no lubricating film to allow the gears to slide more easily, they would not only become extremely hot, but would also wear out quickly. “Without a lubricating film, many things in our everyday lives would be slower, squeakier and jerkier,” explains Prof. Michael Moseler, Head of the Tribology Business Unit at the Fraunhofer IWM. “The electric vehicle would certainly never achieve such a high range,” adds Dr. Kerstin Falk, who heads the “Molecular Lubrication Design” team. Together, they are researching the behavior of lubricating films in highly stressed tribological contacts in order to predict their suitability for low-friction operation. Whether the material in question is metal, plastic or ceramic, ideal lubrication can save over 20 percent energy, as machines run with less resistance. This is also a promising field of research in terms of sustainability.
It is therefore no wonder that the partner companies of the MicroTribology Center µTC, a collaboration between the Fraunhofer IWM and the Karlsruhe Institute of Technology (KIT), are very interested in reducing friction in their systems as much as possible. “Many tribological systems are now being designed at their load limit, where lubricating film thicknesses in the nanometer range and pressures in the gigapascal range occur. Our partners are wondering how to calculate the friction in a component with such highly loaded tribological contacts, as conventional fluid dynamic calculation approaches fail under these extreme conditions,” says Kerstin Falk, summarizing the problem. Together with their simulation team at the MicroTribology Centrum μTC, Falk and Moseler have found an answer to this question. They are now presenting the results of their research in the renowned journal Science Advances.
Understanding and optimizing friction
How friction can be calculated and thus kept as low as possible depends on the lubrication regime a company is aiming for in its components. Usually, it wants to drive its tribosystems — where a force presses the primary and counter bodies together — under elastohydrodynamic conditions. A lubricating film, the thickness of which is much greater than the roughness of the two surfaces, is intended to reduce friction. In this case, the friction can be predicted very accurately using a continuum mechanics approach. This involves solving the so-called Reynolds equation for the lubricant, which Osborne Reynolds derived in 1886.
In addition, the heat conduction equation for the overall system and the linear elastic equations for both surfaces are calculated. The only material data required are the moduli of elasticity and Poisson’s ratios of the friction partners, thermal conductivities and heat capacities of all materials involved as well as accurate constitutive laws — for the density of the fluid and for its dynamic viscosity for a parameter field consisting of pressure, temperature and local shear rate in the fluid. This is state of the art.
However, if the tribological system is operated in boundary lubrication, so with a very thin lubricant film in which the asperity contacts, i.e., the roughness peaks, are only separated by a few atomic layers of the lubricant, only a roughly estimated coefficient of friction is used in the calculations for the “dry” contact points. “This is very unsatisfactory because calculations with guessed material parameters are inaccurate, lead to suboptimal designs and ultimately cost companies a lot of money,” says Michael Moseler.
Kerstin Falk and Michael Moseler were not content with this: Together with four partner companies of the MicroTribology Centrum µTC, they researched their own mathematical law for the behavior of extremely thin lubricating films in a three-year project and developed the Reynolds equation further, so to speak. “We wanted to understand how friction behaves in boundary lubrication,” explains Moseler. The aim of the project is to clarify below which lubricating film thickness the continuum mechanics fails and how the underlying equations can be extended so that a lubricating film thinner than the surface roughness can be calculated. For this purpose, the molecular dynamics of a hydrocarbon lubricant in an asperity contact geometry were calculated, for example two diamond-like carbon (DLC) surfaces lubricated with a polyalphaolefin (PAO) base oil. The results of the molecular dynamics simulation were then compared with those of the Reynolds equation.
The resounding result: For pressures between the friction partners below 0.4 gigapascals and lubrication gap heights greater than 5 nanometers, the Reynolds description agrees well with the molecular dynamics reference calculations, provided that an exact constitutive law for the viscosity of the lubricant is used. In contrast to this, Kerstin Falk and Michael Moseler were able to show that under extreme boundary lubrication conditions, namely high pressures of approx. 1 gigapascal and small lubrication gap heights of approx. 1 nanometer, the sticking of the lubricant to the surfaces is reduced and therefore the slip between a friction partner and the lubricant must be included in the calculation in order to correctly predict the friction. This requires a non-linear wall slip law. This relates the wall slip velocities (i.e., the difference in velocity between a friction partner and the adjacent lubricant) to the local shear stresses in the lubricating film.
Breakthrough in tribology: making boundary friction predictable
With these research results, the researchers are now presenting an innovative method for predicting friction under boundary lubrication conditions. An additional piece of information required for this non-empirical predictive continuum modeling of highly loaded tribological contacts is the atomic structure of the rubbing surfaces. This is determined using in-depth experimental analyses and is a prerequisite for the wall slip law.
The new findings of the Fraunhofer IWM are now being used in follow-up projects to predict friction coefficients and friction behavior in specific applications — for example in gears and bearings — as well as to support the research partners in building up simulation expertise. They can then carry out test bench and component simulations, reduce uncertainties in the design of tribological systems and more precisely determine design parameters. This is an important step towards knowledge-based lubricant, surface and component design and should prove to be extremely interesting for lubricant manufacturers and coaters as well as bearing and gear manufacturers.
Codrignani, A.; Peeters, S.; Holey, H.; Stief, F.; Savio, D.; Pastewka, L.; Moras, G.; Falk, K.; Moseler, M., Towards a continuum description of lubrication in highly pressurized nanometer-wide constrictions: The importance of accurate slip laws, Science Advances 9/48 (2023) Art. eadi264, 17 pp. Link
Press release - Making extremely thin lubricating films predictable (PDF)